Le Kanban logistique est un système visuel de gestion de la production et des approvisionnements en Flux Tirés. Il répond aux exigences du Juste à Temps (JAT), qui a pour objectif de satisfaire la demande client à chaque stade des flux logistiques et industriels : « la bonne quantité de pièces au bon endroit, au bon moment ».
ALBERT DELOIN a développé une méthodologie d’application et une conception de la méthode Kanban s’adaptant à la majorité des activités industrielles. Le Kanban est le « premier » outil d’application de la logique « Flux tirés », fondé sur le principe de production sur besoin. L’objectif de cette méthode performante est de dimensionner les stocks au plus juste. Ainsi la production maîtrise et réduit le coût et les délais.
Venez découvrir nos logiciels implémentant la méthode Kanban.
Méthode kanban : définition et origines
Développée au Japon dans les années 1950 par Taiichi Ōno, ingénieur pour Toyota, la méthode « Kanban » (« étiquette qui informe » en japonais) est à l’origine un système de planification pensé pour la fabrication à flux tendus. Ce système a été fortement inspiré par le secteur de la grande distribution américaine de l’époque. On l’utilise aujourd’hui dans les modèles de production de la Supply Chain qui répondent directement à la demande, tout particulièrement en Flux tirés. Plus concrètement, l’étiquette Kanban matérialise la commande passée par un client qui active elle-même la chaîne de production. Il existe aujourd’hui différents types de kanbans logistiques : le kanban manuel, le kanban électronique ou « e-kanban ».
Qu’est-ce que la méthode kanban pour la chaine logistique industrielle ?
Dans le cadre du pilotage de la Supply Chain, le Kanban est un outil visuel ingénieux. Il permet à la fois une meilleure communication en temps réel et une excellente circulation de l’information. L’étiquette Kanban comporte les informations suivantes :
- Les données générales de l’article : désignation, référence fabricant, code barre et code interne,
- Les données d’approvisionnement : poste client, poste fournisseur, emballage ou contenant, taille du lot, quantité et emplacement.
Au départ, le Kanban se matérialisait par des fiches cartonnées reprenant les informations clés puis accrochées à l’emplacement du produit. Aujourd’hui, et c’est le cas chez Albert Deloin, le système Kanban exploite également des applications informatiques chargées de mettre en place le processus de réapprovisionnement. Ce système peut être représenté sous forme de « tableaux Kanban », composés de plusieurs colonnes où sont positionnées des étiquettes virtuelles. Ainsi, chaque colonne indique le statut de chaque article, les stocks disponibles ou « au contrôle », les encours, etc.
Fonctionnement de la méthode Kanban
Le principe du Kanban dans la Supply Chain est très simple. La méthode repose sur la relation entre les postes « client » et « fournisseur ». Dès qu’une consommation est réalisée par le poste client, l’étiquette Kanban représentant « les pièces consommées » est retournée sur le tableau Kanban du poste fournisseur. Le poste fournisseur étant informé de la réalité de la consommation du poste client, il peut ainsi programmer son prochain réapprovisionnement. Au moment de la fabrication des pièces, le poste fournisseur accroche les étiquettes Kanban sur le contenant finalisé puis expédie l’ensemble au poste client. Ainsi, les cartes Kanban permettent de signaler visuellement les stocks et besoins de réapprovisionnement et d’assurer une bonne traçabilité, grâce à des codes-barres uniques.
Méthode kanban : les enjeux d’une chaine logistique en Flux Tirés
Contrairement au traditionnel système à flux poussés qui agit indépendamment des consommateurs, la méthode Kanban implique un système à flux tirés. Dans ce procédé, il s’agit de limiter la production du poste en amont de la chaîne de travail aux besoins du poste en aval. Ainsi elle ne produit pas plus que nécessaire.
Véritable outil d’exécution Flux tirés quotidien, le Kanban permet d’optimiser les flux logistiques de manière à garantir une production basée sur la demandée réelle du marché exclusivement. La méthode permet ainsi une amélioration de la chaîne logistique en Flux tirés à bien des égards : une meilleure gestion des stocks, une flexibilité accrue face aux variations de la demande et un excellente synchronisation des flux logistiques.
Forces et faiblesses de la méthode kanban “manuel”
Comme toutes les méthodes de gestion logistique, le système Kanban a ses bons et mauvais côtés. Ainsi, des critères pour que son efficacité soit optimale doivent être respectés et certaines conditions sont à prendre en compte. La méthode Kanban est-elle idéale pour votre organisation ? Pour le savoir, voici les forces et des faiblesses du Kanban…
Les avantages du Kanban
Outre son impact sur la baisse des stocks, la réduction des délais, l’amélioration du taux de service, le mérite n°1 de la méthode Kanban consiste en une communication visuelle de qualité et en temps réel pour tous les acteurs concernés par le flux industriel, qui permet de :
- Réduire le gaspillage, la surproduction ou l’excès de stock,
- Améliorer la disponibilité des produits,
- Déléguer aux opérateurs de productions la réalité quotidienne de la production (programmation, fabrication, livraison),
- Donner du temps à l’encadrement pour les tâches du futur. En particulier pour la mise en œuvre des outils du Juste à Temps (S.M.E.D, Poka-Yoke, Qualité Totale, Hoshin, Kaizen, 5S),
- Améliorer la réactivité face à la demande client et aux imprévus,
- Garantir une visibilité efficace et précise concernant le suivi des opérations de fabrication ou d’approvisionnement,
- Faciliter les contrôles qualité, les opérations de maintenance.
Les inconvénients du Kanban “papier”
Comme tous les systèmes, la méthodologie Kanban n’est pas automatiquement la plus adéquate et peut présenter certains inconvénients. Ainsi, le Kanban peut être :
- Difficile à maintenir au-delà d’un certain volume de références,
- Pas adapté à la gestion entre sites éloignés (perte d’étiquettes pour le Kanban manuel),
- Pas adapté à la gestion de produits à la commande,
- Peu apte à fournir des informations statistiques : contrôle CMJ, délais, performance, etc.,
- Aveugle sur l’estimation des charges, etc.
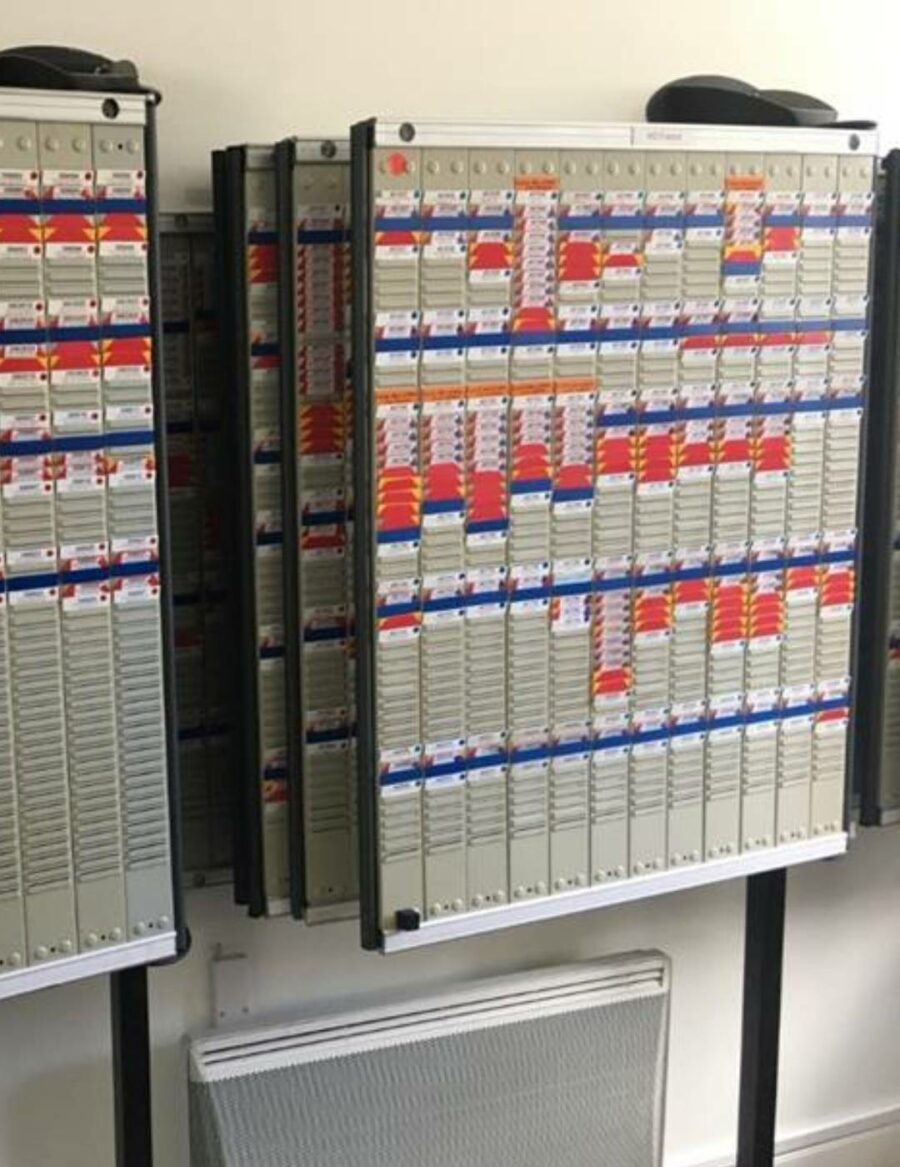
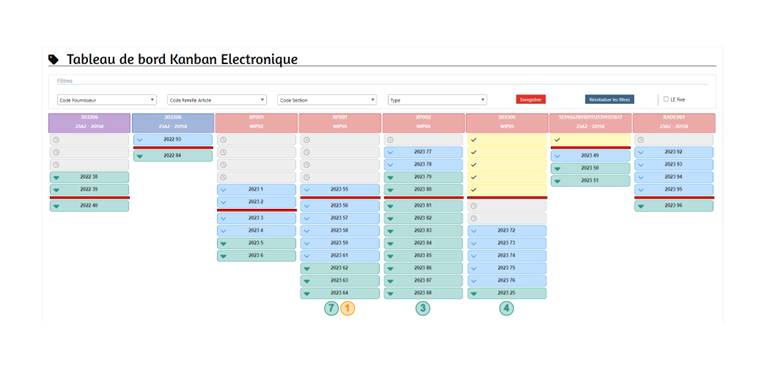
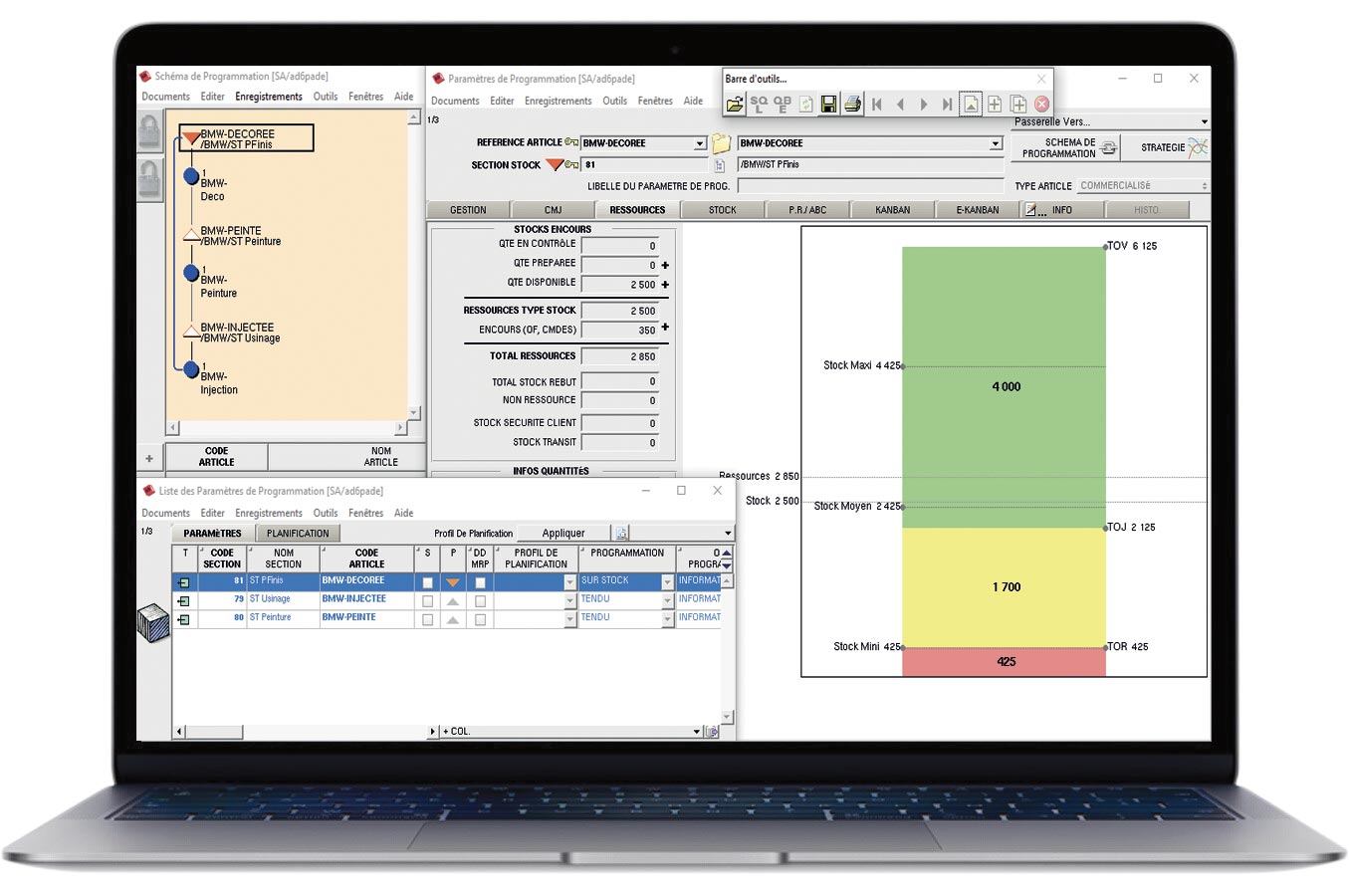
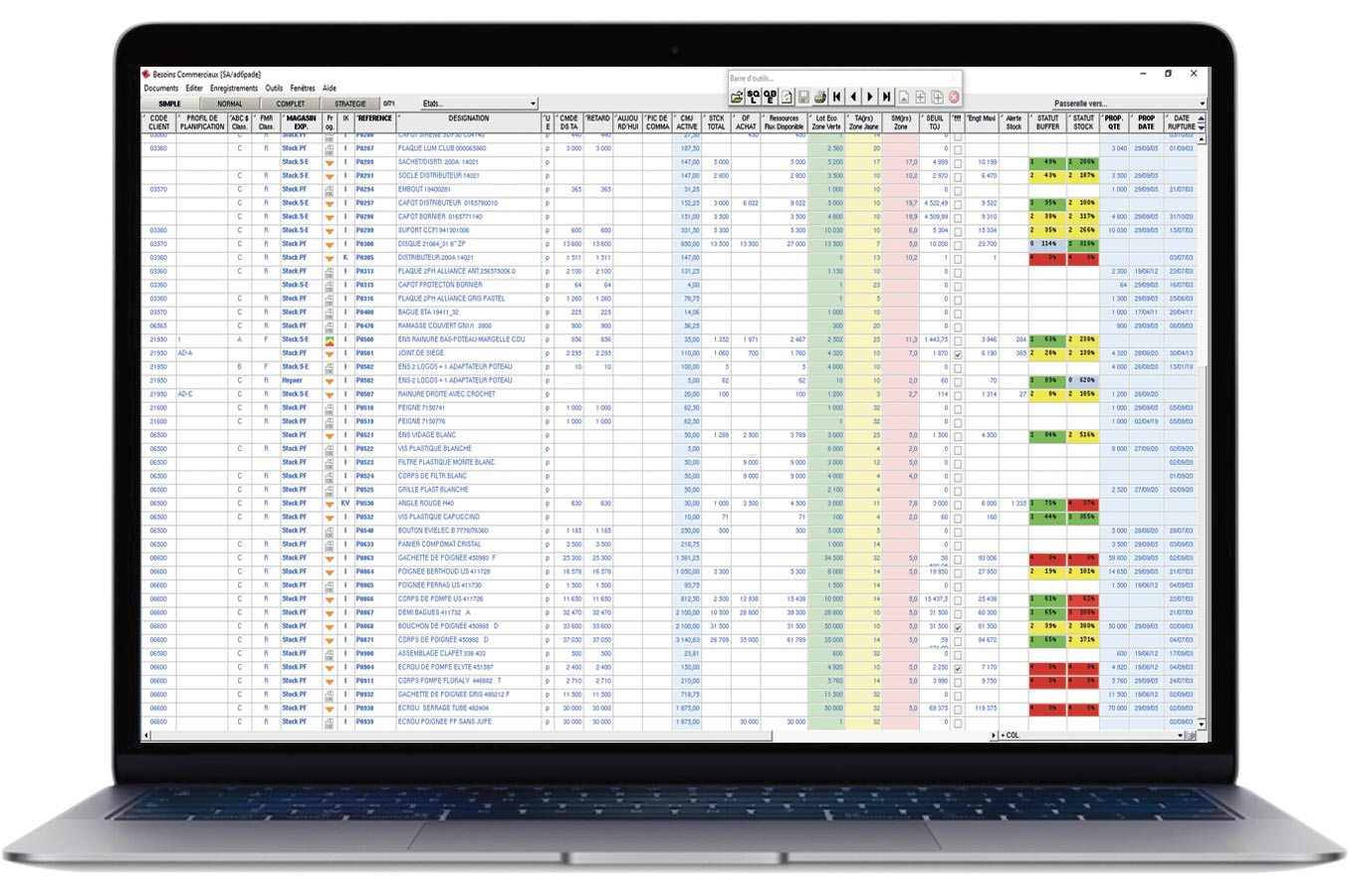
Comment palier aux inconvénients du Kanban « manuel » ?
C’est le point de départ des recherches et développements entamés depuis plus de 30 ans par l’expert Supply Chain. Le fruit de ses travaux s’est concrétisé par le développement de la méthode PFP6, du Kanban électronique « Albert Deloin » et l’intégration de la méthode DDMRP dans la suite de logiciels AD6.
Ainsi aujourd’hui, l’expert Supply Chain propose une offre couvrant l’ensemble du périmètre de planification et pilotage de la supply chain industrielle en « Flux Tirés » à la fois sur le domaine de l’accompagnement au changement et les outils à mettre en œuvre.
Kanban électronique (ou virtuel) ou e-Kanban
Grâce à un déclenchement informatisé, une matérialisation « étiquette Kanban » imprimée à dessein (avec Code-Barres ou RFID), le Kanban virtuel se substitue à l‘OF. Il offre tous les avantages du Kanban en écartant la majorité des inconvénients s’il est intégré à un outil complet de pilotage de la Supply Chain tel que les logiciels de la gamme AD6.
Les Kanbans électroniques s’impriment à proximité du « producteur ». Ils sont associés (collés) sur les cartons et consommés (détruits) lors de leur consommation. Chacune de ces actions fait l’objet d’un message qui permet de suivre le cycle de vie de l’étiquette Kanban.
Comparable au Kanban électronique, le e-Kanban permet de mettre en œuvre des boucles Kanban entre Clients et Fournisseurs externes
Kanban “informatique”
Les règles (paramètres, déclenchement, etc.) du Kanban « informatique » sont similaires au Kanban traditionnel. En revanche, il n’y a plus d’étiquettes et les tableaux de bord de pilotage informatique remplacent les plannings (cf. logiciels AD6 et méthode PFP6).
Venez découvrir nos logiciels implémentant la méthode Kanban.
Méthodologie kanban en logistique : quand l’utiliser ?
Au-delà, de la littérature courante, tous les domaines d’activité industrielle ou de négoce, traitant des produits répétitifs en grandes, moyennes ou petites séries, peuvent appliquer la méthode Kanban.
Il est pourtant courant de lire que le Kanban convient davantage à un système de fabrication massive avec peu de variations, et souvent les conditions suivantes doivent être remplies :
- Une production en continu,
- Un haut degré de standardisation et de synchronisation des produits,
- Une stabilité dans la production,
C’est totalement faux ! Et c’est même le contraire ! Le Kanban et plus généralement les Flux Tirés font une énorme différence avec les autres systèmes en particulier dans le mode d’aujourd’hui qui est « volatile, incertain, complexe et ambigu ». C’est la définition de l’acronyme VUCA : Volatility, Uncertainty, Complexity and Ambiguity.
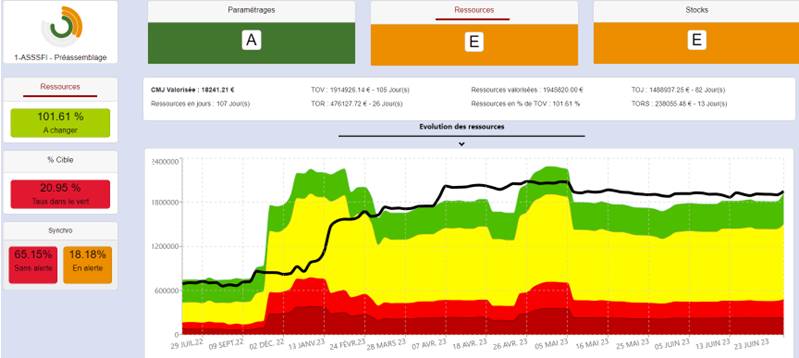