“Il n’y a pas de pire gaspillage que de produire quelque chose dont vous n’avez pas besoin immédiatement et de le stocker dans un entrepôt. (…) Avant, nous pensions que le premier processus de fabrication (amont) envoyait les pièces au stade suivant de production (aval). (…)
Mais nous avons décidé d’inverser ce processus et de considérer ce qui se produirait si les derniers stades devenaient les premiers et s’ils n’utilisaient que le matériel nécessaire à cet instant. (…)”
Taïchi Ohno – Ingénieur Toyota
Les organisations flux poussés (MRP) et flux tirés
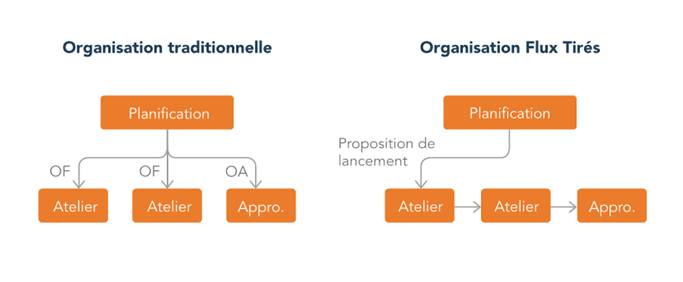
Définition et fonctionnement MRP (Flux Poussés)
Aujourd’hui, la planification des activités de production et d’approvisionnements est de plus en plus compliquée : les délais demandés par les clients se réduisent, l’exigence en qualité et en respect des délais augmente, les catalogues de produits grossissent, leur durée de vie est de plus en plus courte et l’horizon prévisionnel diminue. Pour autant, le mode de pilotage majoritaire des flux industriels est toujours le MRP, un modèle développé durant les années 50, à une époque où on vendait ce que l’on fabriquait (la demande était supérieure à l’offre).
Le modèle flux poussé (MRP) repose sur la capacité à prévoir et à planifier. Devant l’augmentation de la variabilité de la demande (et donc des prévisions), le raccourcissement des horizons d’analyse, les « calculs de besoins » sont exécutés de plus en plus souvent (jusqu’à 2 fois par jour), les sécurités* ont été augmentées et on ne cesse d’améliorer la justesse des prévisions.
Le constat reste pourtant toujours le même : des stocks déséquilibrés
- Des manques et des ruptures pour les produits nécessaires,
- Des surstocks pour les produits inutiles
De surcroit, l’accroissement de la fréquence de lancement des calculs de besoin a entrainé
- Un accroissement du volume de travail à l’ordonnancement et la planification,
Et pour les ateliers et les approvisionnements, des instructions contradictoires
* Le paramétrage du calcul de besoin MRP autorise :
- L’utilisation d’un Stock de sécurité : quantité statique (saisie) qui déplace le zéro du calcul de besoin net.
- Point de commande : valeur statique (saisie), révisée à fréquence « relative ». L’atteinte de ce seuil déclenche un Ordre de fabrication ou d’approvisionnement. L’utilisation de « points de commande » crée une rupture dans le calcul de besoin avec les niveaux amont.
L’organisation Flux poussé (MRP) : un modèle qui a atteint ses limites dans la supply chain actuelle
Pour compléter le tableau, la multiplicité des produits, la diminution de leur durée de vie et même leur complexité impose un volume de travail important pour les équipes en charge de maintenir les données techniques, dont la qualité est un pilier du fonctionnement du modèle MRP (Les composants de la nomenclature sont tous dépendants). Il est très courant de rencontrer des entreprises qui ont au fil du temps laissé dériver les données techniques. Les décisions sont alors prises en dehors de l’ERP (sous Excel) et réinjectées dans l’ERP.
Pourquoi cette situation ? Parce que l’horizon de calcul du MRP est supérieur à la somme de tous les lead time, de la production du produit fini jusqu’aux approvisionnements extérieurs. Ainsi, le prévisionnel des ventes, indispensable au MRP, couvre plusieurs mois, voire plusieurs trimestres… On voit donc que par nature le modèle MRP n’est plus adapté au monde actuel : les décisions prises aujourd’hui seront contredites demain, avec pour conséquence : Un effort important et constant des équipes en charge de piloter la Supply Chain pour une performance décevante.
Pour pallier les défauts du MRP, les entreprises ont recours à des APS. Leur fonction première est d’optimiser l’ordonnancement des ordres de fabrications de manière à réduire les temps de traversée et mieux utiliser les ressources industrielles. Dans la majorité des cas, sans remettre en cause la qualité de ses outils, l’effet est décevant. Pourquoi ? Parce que les APS ne décident pas de ce que l’on lance en production (ce n’est pas leur fonction). Ils optimisent les décisions « déjà » prises. En somme, ils interviennent trop tard.
Il faut donc revoir la copie et penser autrement pour atteindre le Juste-à-Temps. Comment ?
En implémentant une organisation et un pilotage « Flux Tirés » de la Supply Chain.
Philosophie « Flux Tirés »
L’organisation « Flux Tirés » a été pour la 1ère fois formalisée par Taichi Ohno (Ingénieur Toyota et père du TPS) notamment avec le développement de la méthode Kanban :
« Il n’y a pas de pire gaspillage que de produire quelque chose dont vous n’avez pas besoin immédiatement et de le stocker dans un entrepôt. (…) Avant, nous pensions que le premier processus de fabrication (amont) envoyait les pièces au stade suivant de production (aval). (…) Mais nous avons décidé d’inverser ce processus et de considérer ce qui se produirait si les derniers stades devenaient les premiers et s’ils n’utilisaient que le matériel nécessaire à cet instant. (…) »
Les principes de fonctionnement de l’organisation « Flux Tirés »
- Seul le besoin aval provoque la quantité à produire ou à approvisionner par l’amont,
- L’ensemble des flux industriels est décomposé en relations Client/Fournisseur,
- Chaque relation Client/fournisseur est définie par un jeu de paramètres et une formule de calcul.

Les paramètres “Flux tirés”
CMJADU | Consommation Moyenne Journalière
Elle dimensionne par produit la relation client-fournisseur et est définie sur une période représentative de l’activité de l’entreprise. |
LEEQ | Limite d’Engagement ou Lot Economique Série de lancement du fournisseur. Elle peut être exprimée en quantité ou en jours. |
TALT | Temps Alloué par le fournisseur (Lead Time) Délai nécessaire pour programmer, fabriquer et livrer le client (atelier ou magasin).Exprimé en jours. |
SMMSS | Stock Minimum (Sécurité)
Sécurité pour répondre aux fluctuations de la demande. Exprimé en jours ou en % du TA (délai). |
Les formules de calcul du flux tirés
- Soit R les ressources : R = Stocks + Encours
- Soit S le seuil de déclenchement : S = (TA + SM) x CMJ
Ainsi, si R < S, alors il est temps de lancer une fabrication ou un approvisionnement de LE pièces.
Le découplage par les stocks
La mise en place d’une organisation « Flux Tirés » correspond donc à décorréler la demande (l’aval) du producteur (l’amont) en pilotant dynamiquement un stock tampon entre les deux :
- Simplification : Décomposition du flux en niveaux « indépendants »,
- Réactivité : le positionnement d’un stock de découplage permet de « casser » le délai,
- Synchronisation : chaque niveau travaille au même rythme grâce à la CMJ.
La CMJ permet de redimensionner, en temps réel, l’ensemble des flux. - Robustesse : l’indépendance des niveaux empêche la propagation des erreurs.
Exploitation des paramètres
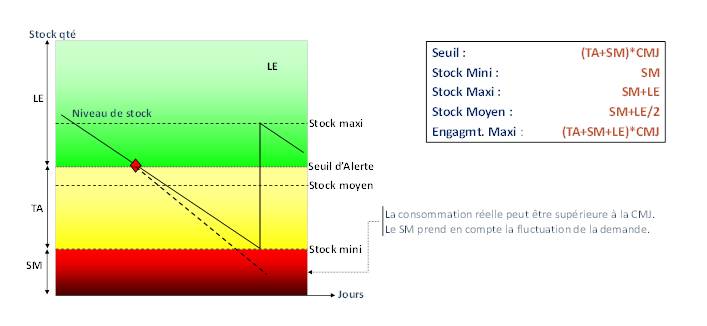
Pilotage « Flux Tirés » : où le mettre en œuvre ?
Au-delà, de la littérature courante, tous les domaines d’activité industrielle ou de négoce, fournissant des produits en grandes, moyennes ou petites séries, peuvent fonctionner en Flux Tirés.
Il est pourtant courant de lire que le Kanban convient davantage à un système de fabrication massive avec peu de variations : production en continu et stabilisée, haut degré de standardisation et de synchronisation des produits, …
C’est totalement faux, et c’est même le contraire !
L’organisation « Flux Tirés » prend toute sa valeur dans des conditions « volatiles, incertaines, complexes et ambiguës », et son efficacité fait une énorme différence avec tous les autres systèmes.
Flux poussés (MRP) vs Flux Tirés : quelle différence fondamentale ?
Pour conclure, le pilotage « Flux Tirés » ou MRP (Flux Poussés) de la Supply Chain utilisent les mêmes données d’entrée. Alors, quelle est la différence fondamentale entre les deux méthodes ?
Dans un fonctionnement MRP, les prévisions déclenchent les lancements (Ordres de fabrication, d’approvisionnement, …), alors que dans une organisation « Flux Tirés » elles servent à dimensionner un niveau d’activité. Les lancements sont déclenchés par la réalité des livraisons et consommations.